The D136-001-007 is a servo drive produced by MOOG, which measures the flow of hydraulic oil according to an input electrical signal or command, thereby controlling the position, speed, pressure or force in a certain type of machine or equipment (generally through a piston or plunger).
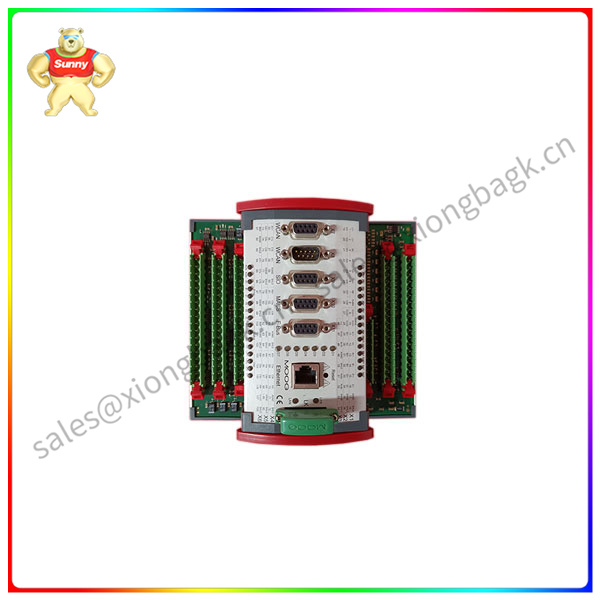
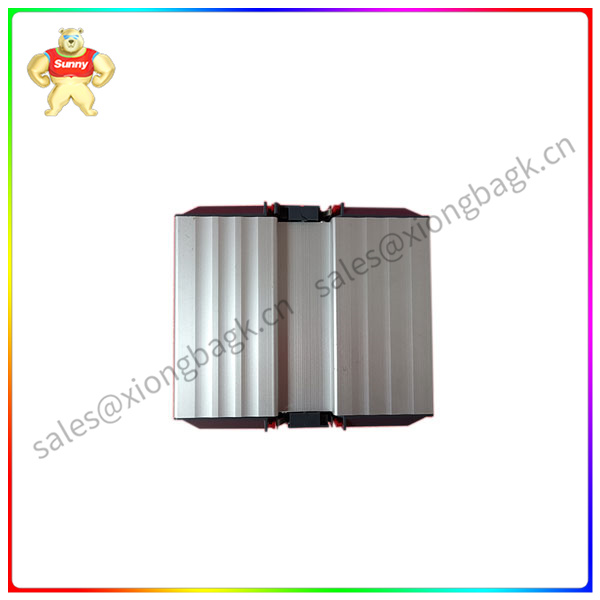
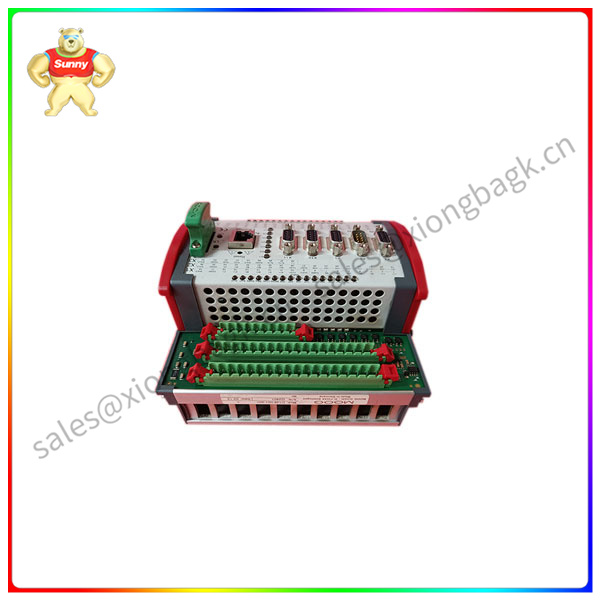
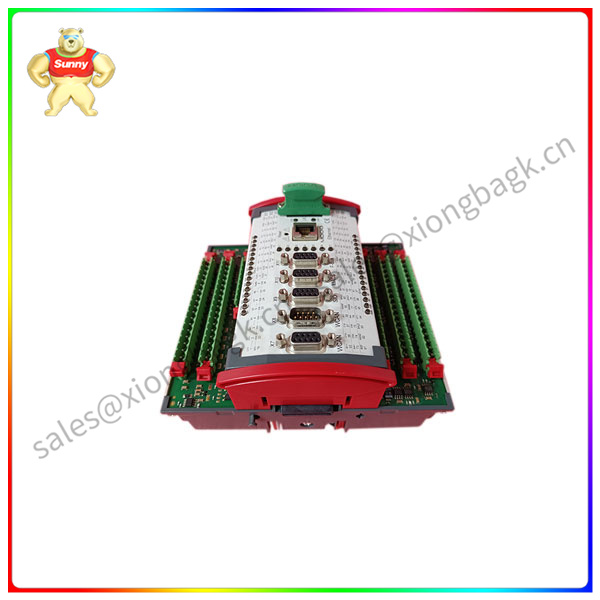
Moog offers a wide range of freely programmable motion controllers, each designed with specialized features to meet a range of customer requirements. Whatever your petition, we have a motion, okay
The controller will meet your requirements. MSC 1 and MSC 1 motion controllers
MSC 1 and MSC I motion controllers high
The high performance motion controller with the function of a bribery PLC is ideal for complex centralized and distributed applications. These modules are all designed for similar tasks, with different interfaces and performance. These movements
The controller has built-in P20 protection and is mounted on a DIN rail in the electronic cabinet.
The MSC Motion controller provides resolution analog input/output and position sensor interfaces. It is designed for fast and accurate two-axis closed-loop control. The MSC Motion controller is best suited for the need to pass simulation
The interface controls the application of one or two actuators.
The msclI motion controller has multiple fieldbuses
Interface and four position sensor interfaces. It is designed for closed-loop control, with or without the profile generation of multiple electric or hydraulic shafts.
The combined capabilities of the msc and msclI motion controllers can be extended with additional high-resolution analog and digital /0 and communication modules. The expansion module clips to the side of the motion controller and extends through the interior.
Bus (E-Bus) for electronic connection.
To control complex decentralized applications, two can bus interfaces are included.
Servo driver is also known as "servo controller", "servo amplifier", is used to control the servo motor of a controller, its role is similar to the frequency converter acting on the ordinary AC motor, is a part of the servo system, mainly used in high-precision positioning system. Generally, the servo motor is controlled through three ways of position, speed and torque to achieve high-precision transmission system positioning, which is a high-end product of transmission technology.
Servo D136-001-007 drivers are electronic devices made of circuit boards, microchips, wires and connectors. They are attached to the motor to control its rotation. They can make the motor speed up, slow down, stop, and even go backwards at any time. This is achieved by controlling and directing the current of the D136-001-007 motor wires. Without a servo drive, the motor may spin uncontrollably or not at all. Some servo drives control small motors, such as the elbows of robotic arms. Other servo drives control large motors, such as the wheels of heavy machinery or electric vehicles. More powerful motors require more powerful servo drives.
How does the servo drive work and what causes the motor to D136-001-007 spin? One of the components will have conventional magnets, while the other will have windings or "electromagnets" that turn them on by running an electric current through them. The rotating magnetic effect can be obtained by continuously opening and closing different windings. This pushes the conventional magnet, causing the rotor to spin. Brushed motors have windings in the rotor and magnets in the stator, while brushless motors have windings in the stator and magnets in the rotor. The servo drive controls the torque, speed and position of the motor shaft by adjusting the supplied current and voltage.